无尘投料站作为粉体物料处理的关键设备,其能耗直接影响生产效率和运营成本。优化能耗需从智能控制和空压机维护两方面入手,结合技术创新与系统性管理,实现降本增效。
一、智能控制系统的应用
无尘投料站的能耗浪费多源于设备空转、过量供气或非必要运行。通过引入智能控制系统可显著改善这一状况:
1.实时监测与动态调节:智能传感器可监测物料储量、气流量和设备状态,自动匹配投料速度与供气量。例如,当物料不足时,系统自动降低风机功率;物料堆积时,启动振动破拱功能,避免电机过载耗能。
2.预约定时与任务排程:通过中央控制系统设置生产计划,使投料站按需启动。例如,在夜班低峰时段集中完成非连续工艺的投料任务,减少设备待机能耗。
3.能耗数据追溯与分析:智能平台记录历史数据,分析高耗能环节(如频繁启停、气压波动),并提供优化建议,助力持续改进。
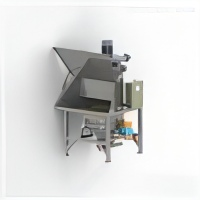
二、空压机维护与能效管理
空压机是无尘投料站的核心动力源,其能效直接影响整体能耗:
1.定期维护保障高效运行:清理或更换进气过滤器可减少进气阻力,降低压缩机功耗;检查冷却系统效率,避免高温导致能耗上升;校准压力传感器,确保供气压力稳定,避免过高或过低造成的浪费。
2.智能空压机控制:采用变频空压机,根据实时需求调节转速,取代传统定频设备的恒速运行模式,节能效果达20%-30%。
3.余压回收技术:将投料站排空时的剩余压缩空气用于除尘或其他辅助设备,提升能源利用率。
通过智能控制与空压机维护的协同优化,可显著降低无尘投料站的能耗。企业需结合自身工艺特点,定制技术方案,并建立长效监测机制,持续提升设备能效。这不仅节省运营成本,更符合绿色制造发展趋势,增强市场竞争力。